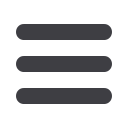
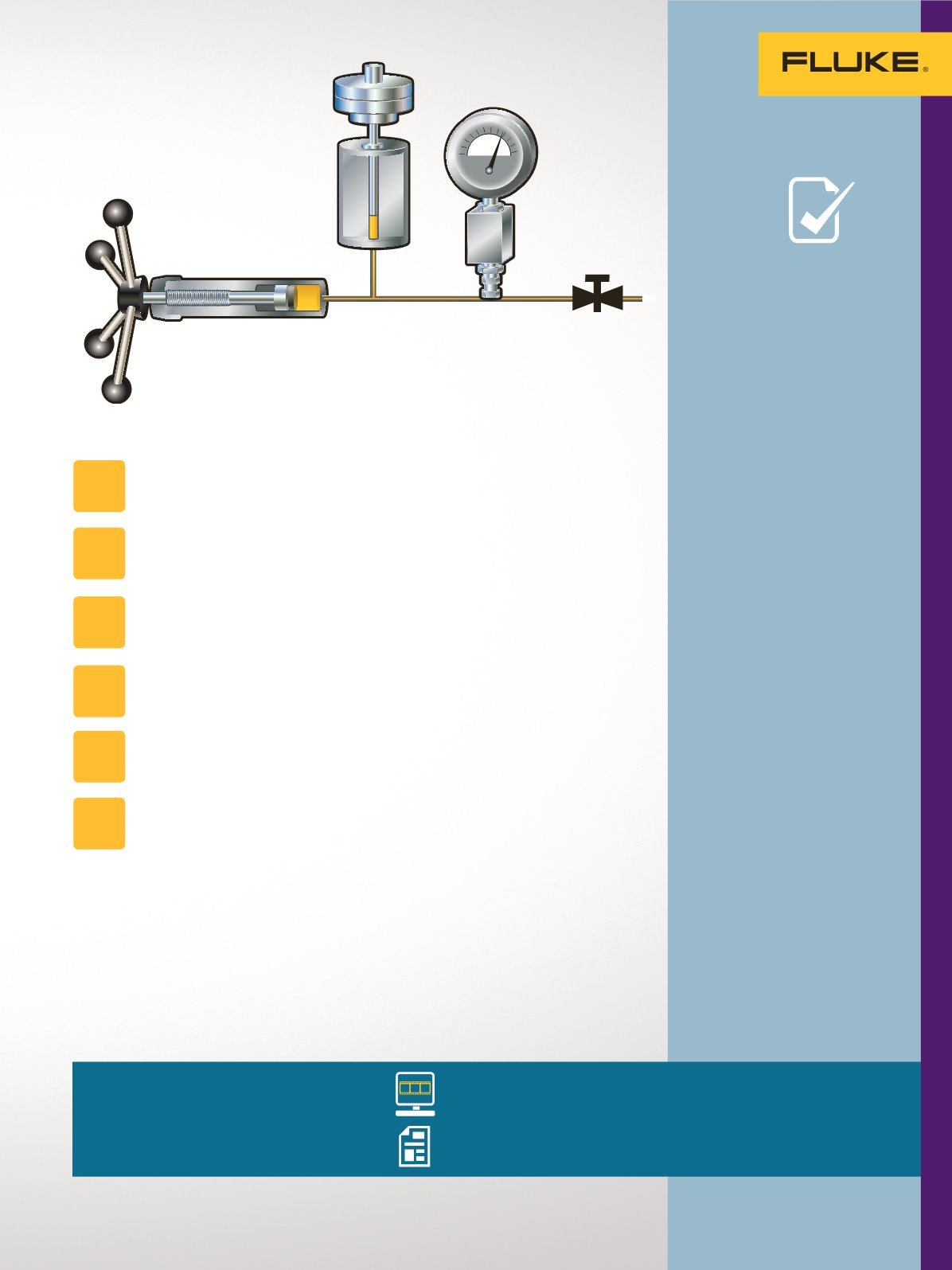
50%
0%
100%
The pressure gauge should be mounted in the same orientation
(vertical or horizontal) as in the process.
Measurement points should be distributed uniformly over the
calibration range.
Calibrated weights are placed on the instrument corresponding
to the measurement points.
Pressure is added with an internal pump or screw press until the piston
holding the weights begins to float.
The piston and weight are spun by hand to minimize friction.
While the piston is floating the reading on the device under test is com-
pared to the pressure corresponding to the sum of the selected weights.
•
Deadweight tester
weights are calibrated to
match a wide range of
pressure units.
•
Local gravity often is the
largest factor affecting
accuracy. Use Fluke
PRESSCAL software to
achieve accuracy of
+/- 0.008%.
•
To increase the number of
available set points, use
incremental weight sets.
•
Forgo wrenches or PTFE
tape by using adapters to
fit multiple sizes and types
of devices with leak tight
seals to 20,000 psi.
•
Safety First! Choose fittings,
tubing and seals with
pressure ratings above the
full scale of the instrument.
•
Hydraulic systems are
preferable to gas systems
for pressures above 2000
psi due to safety and ease
of use.
•
Consider achieving
cleanliness using distilled
water as a media or use a
liquid separator from Fluke
instead of gas.
•
Lubrication can improve
performance by using oil
when it is allowed.
STEP
1
STEP
2
STEP
3
STEP
4
STEP
5
STEP
6
To perform the test:
Additional resources
For more in depth information about
this application check out these videos
and application notes from Fluke.
Check out the 700G videos.
700G Data Sheet.
Interpreting Specifications for Process Calibrators, Application Note
TECH
TIPS
39
Pressure Applications