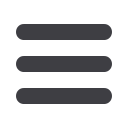
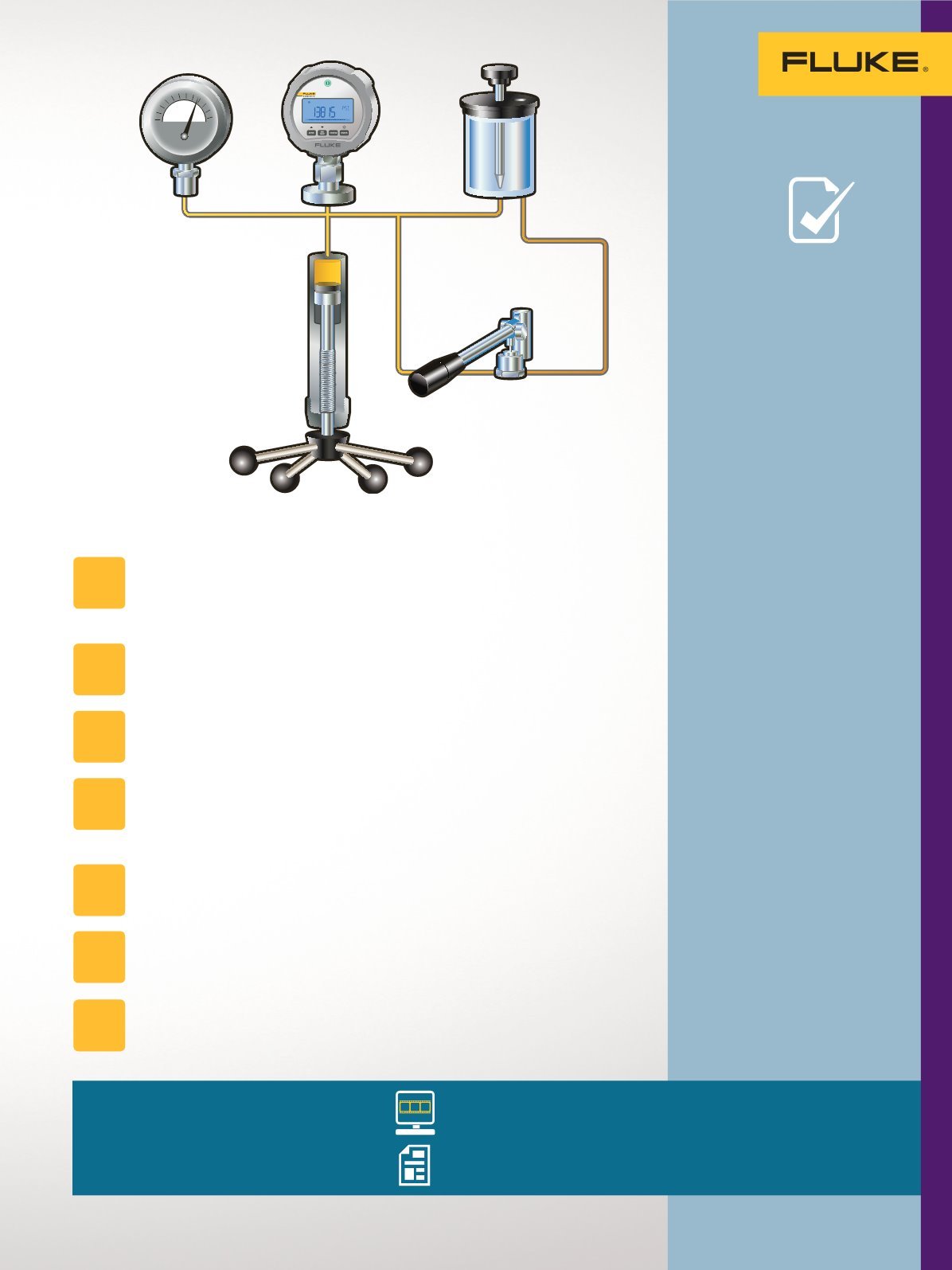
TECH
TIPS
2000PSI
148BAR
50%
0%
100%
The pressure gauge should be mounted in the same orientation
(vertical or horizontal) as in the process. An angle adapter such as the
P5543 may be used.
The reference pressure gauge (2700G) should be mounted such that the
display is easily seen.
For hydraulic comparators prime the fluid with the priming pump,
to remove any bubbles.
Measurement points should be distributed uniformly over the calibration
range. Conveniently source pressure with a manual pump up to 300 psi,
after that use an external pressure supply.
For gas comparators use the fine needle valve or fine adjustment screw
press to precisely meter the pressure.
With hydraulic models use the screw press to source and fine adjust
the pressure.
The source pressure can be adjusted until the device under test is
reading a nominal pressure or until the reference gauge reads the
nominal pressure.
•
Use a reference gauge with
better accuracy to meet test
uncertainty ratios over a
wider range of pressures.
•
Forgo wrenches or PTFE
tape by using adapters to
fit multiple sizes and types
of devices with leak tight
seals to 20,000 psi.
•
Safety first! Always use
fittings, tubing, and seals
with pressure ratings above
full scale of the instrument.
•
If possible use oil for better
lubrication.
•
Use gas to improve
cleanliness or a liquid-to-
liquid separator available
from Fluke.
•
Hydraulic systems are
preferable to gas systems
for pressures above
2000 psi due to safety
and ease of use.
STEP
1
STEP
2
STEP
3
STEP
4
STEP
5
STEP
6
STEP
7
To perform the test:
Additional resources
For more in depth information about
this application check out these videos
and application notes from Fluke.
Check out the 700G videos.
700G Data Sheet.
Interpreting Specifications for Process Calibrators, Application Note
41
Pressure Applications