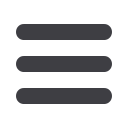
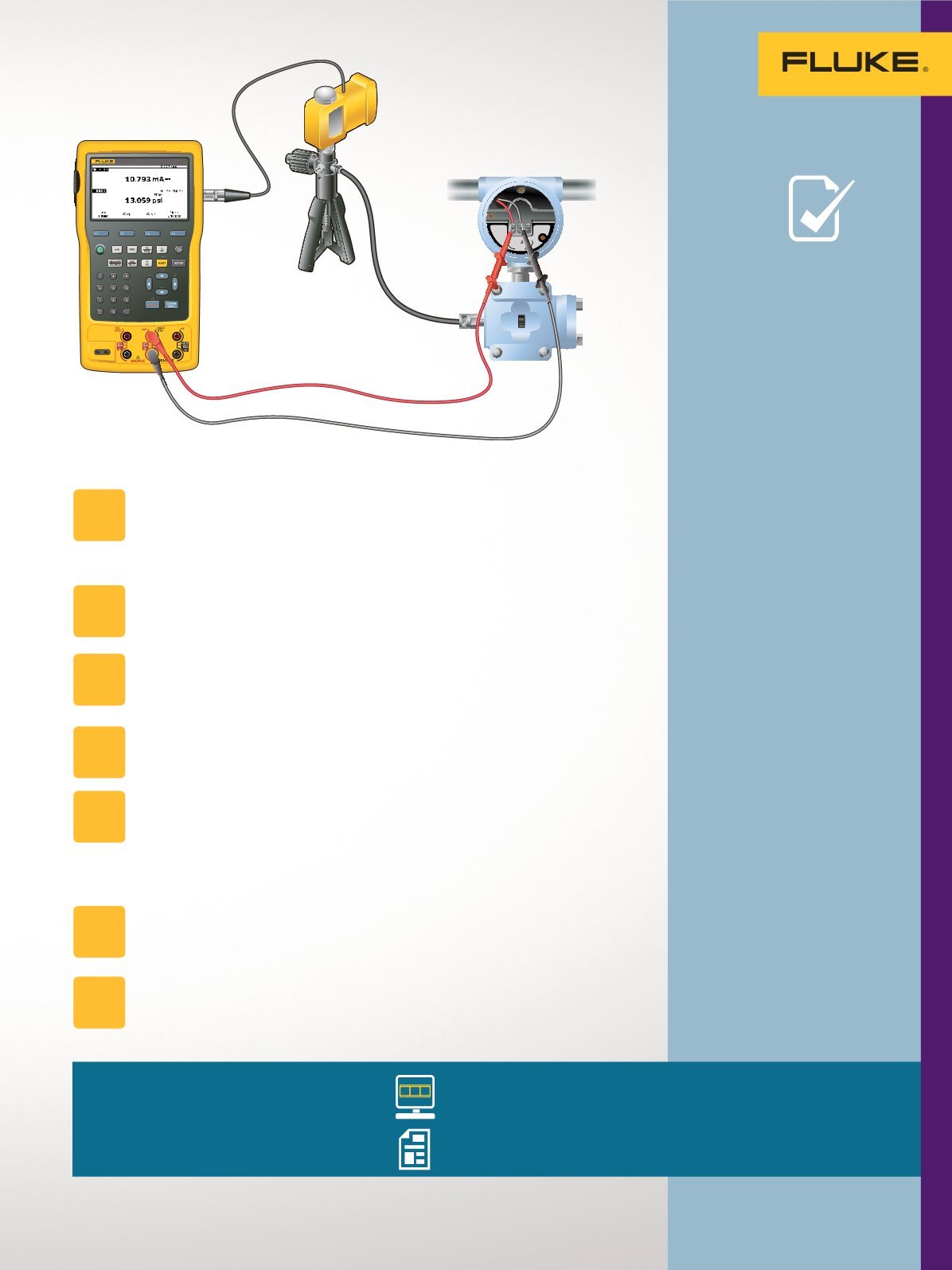
Hand
Pump
Pressure Input
mA Measure, 24V Loop
Pressure
Module
754
DOCUMENTINGPROCESSCALIBRATOR
+ – –
TEST
PWR/
COMM
Sometimes it is necessary to trim
the input sensor of the transmit-
ter more than once. It is critical
that the pressure module be ze-
roed before test and adjustment.
For best ßadjustment success:
•
After pressing Fetch for
the pressure measurement,
select the trim button quickly
before the pressure measure-
ment changes.
•
Give the measured
mA
and
pressure time to settle for best
measurement results.
•
Always de-bug the pressure
test setup for leaks in the
shop before going to the
field, including installing the
pressure module connection
adapter to the hand pump.
•
If the full scale value of the
transmitter is less than 25 %
of the full scale of the pres-
sure module, select a lower
range pressure module for
best results.
•
If performing higher
pressure calibrations with a
hydraulic pump, use the cor-
rect fluid such as mineral oil
or de-ionized water. Standard
tap water will leave deposits
in the pump and cause
erratic operation, leaks or
difficulty priming.
•
If the pass/fail accuracy is set
at the limits for the transmit-
ter, adjust the transmitter if
the errors are greater than
25 % of limits.
•
If the errors are less than
25 % of limits, it might be best
to not adjust the transmitter
as adjusting might make it
less accurate.
Isolate the transmitter from the process being measured and its loop
wiring. If measuring the mA signal across the transmitter test diode
leave the wires intact, but note this method does not give the best mA
measurement accuracy.
Connect the mA measurement jacks of the 754 to the transmitter.
Connect the pressure module cable to the 754 and connect the
transmitter test hose from the hand pump to the transmitter.
Press the HART button on the calibrator to see the configuration of
the transmitter.
Press HART again and the calibrator will offer the correct measure/source
combination for the test. If documenting the calibration press As-Found,
input the test tolerance and follow the prompts. If the measured mA signal
at the test points is found within tolerance the test is complete. If not,
adjustment is required.
Select adjust and trim the transmitter’s pressure zero, mA output signal
and input sensor.
After adjustment select As-Left, document the condition of the transmitter
after adjustment and if the test passes, it is complete.
STEP
1
STEP
2
STEP
3
STEP
4
STEP
5
STEP
6
STEP
7
To perform the test:
Additional resources
For more in depth information about
this application check out these videos
and application notes from Fluke.
See the smart pressure calibration video at:
www.fluke.com/pressurevideoHART Smart Transmitter calibration application note at:
www.fluke.com/smarttranappnoteTECH
TIPS
27
Pressure Applications